Legacy Control System Migration
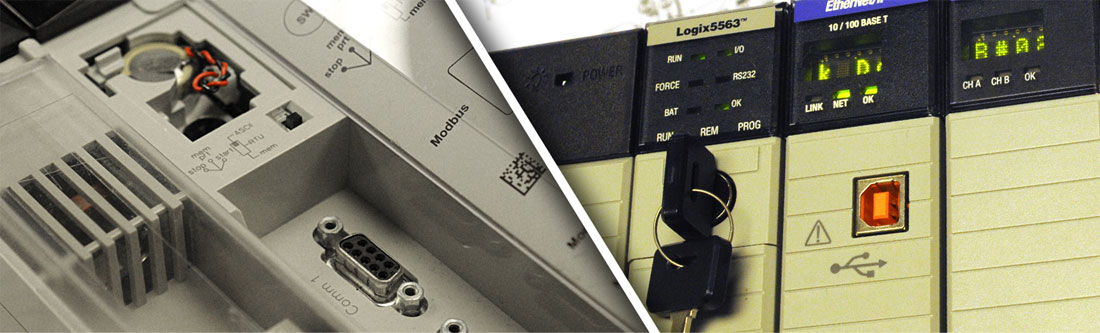
The Challenge:
Convert a Legacy Modicon Process Control System to a Rockwell ControlLogix Platform
Many clients are facing the challenge of migrating legacy systems to new technologies—to take advantage of increased functionality and performance plus decreased maintenance cost and downtime. This client, a global manufacturer of household products, asked MidStates to upgrade a large process control system from a legacy Modicon system to a Rockwell ControlLogix platform.
A key objective was to retain their large network of existing I/O modules, avoiding the considerable engineering time, expense and downtime of replacement, while realizing the benefits of a modern control platform. To accommodate their budget and aggressive production schedules, we would need to complete the project in phases, with no downtime. Each phase would entail transferring a section of the control system logic to the ControlLogix PLC, while the original control stayed intact.
The Existing System:
The existing system consisted of a Modicon Quantum PLC with more than 1000 I/O points distributed across six Quantum and 800 series I/O racks. The controller communicated with several other Modicon and Rockwell PLCs via Ethernet, Data Highway Plus (DH+) and Modbus Plus networks to provide interlocking with other process systems. Several Wonderware InTouch HMIs provided the operator interface to the system with a Wonderware Historian providing the required data logging and reporting.
Initial Engineering:
We approached the conversion in phases, with all I/O modules in place and operational. The team kept field wiring connected to the Modicon I/O modules, with the original PLC remaining online until all programming was transferred to the new PLC. We employed a customer-specific technique to maintain connection between the two PLCs, including diagnostics to help place all equipment into a safe state in the event that communication was lost. Programming added to the original PLC allowed control for each device to be quickly switched between PLCs. This provided the structure for converting sections of logic in phases. We also devised a contingency plan that would allow control to be temporarily switched back to the legacy PLC, if needed, any time during the process.
Startup – Phase I:
While the system was still being controlled by the Modicon PLC, the ControlLogix processor was installed and the dedicated network connection to the Modicon processor was established. We completed network testing to validate reliability and speed. We then tested HMI and Historian communication to the new PLC.
Startup – Phase II:
Prior to switching control to the new Rockwell ControlLogix platform, we conducted process simulation testing of the PLC; this included verifying each signal between the new and old processor. With this process complete, we had a very high level of confidence that the conversion would be accomplished quickly.
Startup – Phase III:
We switched control to the new PLC and tested I/O for each device during a four-hour lull in production. We also completed comprehensive device testing, starting from device controls on the HMI through the new PLC-PLC network connection and out to the field devices. After each device was tested, the system was placed into production.
Project Status:
According to the strategic plan formed with the client, we have successfully moved the initial section of control to the new PLC. As the remaining logic is converted and moved to the ControlLogix PLC, the original Modicon I/O racks will be replaced with 1756 ControlLogix racks. MidStates' engineers designed the new program for easy transition from the Modicon I/O to Rockwell I/O system.
Do you need to migrate a legacy system to a modern platform? Not sure where to begin? MidStates engineers will partner with you, creating a customized migration plan that fits your budget, timeline and production requirements. We can help protect your current process while facilitating a smooth migration to a modern system, then provide ongoing support.
No system is too small or too large; from ten to 10,000 I/O points, all conversions receive careful attention to planning, testing and commissioning. To discuss your challenge, please contact MidStates Controls.